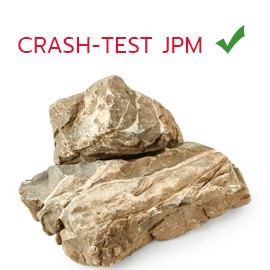
ROBUST
Its structure and mechanical resistance are identical to those of the steel tipper. And there is no risk of rust.
Its structure and mechanical resistance are identical to those of the steel tipper. And there is no risk of rust.
The most robust welding technique on the market.
Double safety device and handle incorporated into the sideboard, thus preventing unexpected opening by collision
196 kg of additional payload for a 3260 mm mixed aluminium tipper and even 236 kg of additional payload (!) for an all aluminium tipper compared with their steel equivalents.
Over the last 10 years the JPM fleet in circulation in Europe represents 20,000 aluminium bodies.
0.5 l/100 km fuel savings with JPM aluminium bodywork (compared with its steel equivalent).
The net dumping capacity of a 3300 mm tipper is 4T3 (load uniformly distributed). We guarantee at least a net dumping capacity of 2T whatever the position of the load in the tipper (e.g. the whole load at the front).
The taper of the JPM pillar provides an efficient hold. The clamping screw makes it possible to take up any clearance which could appear over time. The pillar doesn't move and contributes to the long life of the tipper.
Double safety tall hinge
The primer and the thermosetting resin-based epoxy powder paint make a very resistant 120 µm layer.
Articulation with bumper (no pin)
Tool-free assembly and dismantling
Travel stop for the sideboard
On closing the lip settles on the platform thus providing better retention of fine loads like sand.
It is possibleto lash on the outer frame return along the entire length of the bodywork.
The rear aluminium rollers are fitted on a self-lubricating ring.
The door unhooks when the tipper is at 15°. Unhooking takes place by a direct connection of the tipper with the hook (no chain, or cable or tie rod).
Customise your JPM tipper very simply: order options via our store and fit them easily and quickly. In this way you have a tipper customised to your professional requirements. In spite of everything, this same tipper can evolve. It can be customised in a different way at any time.
Collision or an unfortunate impact with a bucket can happen quickly on a site. Carry out repairs yourself in record time: order your door or your sideboards with just a few clicks on the JPM website.
The impact of an aluminium body on the environment is 20% less than that of its steel equivalent.
2 years’ guarantee on purchase of the tipper
+ 1 additional year free when registering the tipper guarantee on our website
+ 2 additional years on sale on our website
BODYWORK |
• Tipper platform in high quality aluminium sheet: 5083 H16 thickness 3.5 mm |
SUBFRAME |
• Aluminium profile tipper, thickness 4.5 to 12 mm |
SAFETY |
• Safety solenoid valve on cylinder |
FINISH |
• Shot blasting + 60 μm powder primer + 60 μm powder paint |